Polymer membranes could benefit from taking a dip
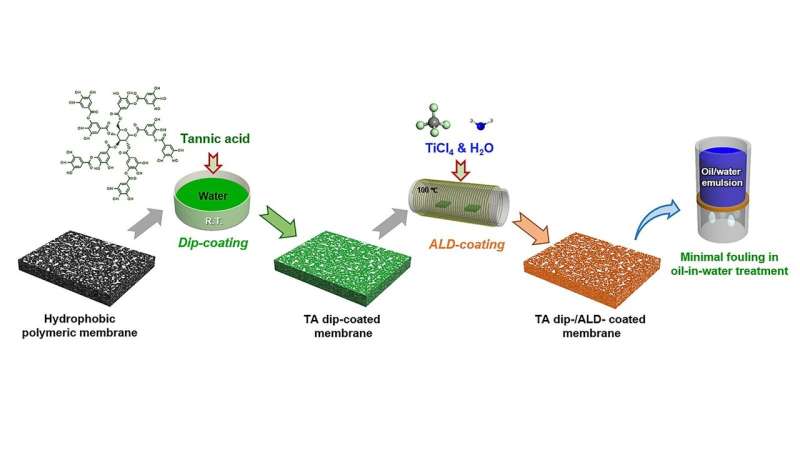
Many industrial processes rely on thin membranes that can clean water, for example, by filtering out impurities. In recent years, a technique called atomic layer deposition (ALD) has been used to tune these membranes for better performance, but there's a hitch: Many of them are made from materials that aren't compatible with ALD, a process using alternating chemical vapors to create very thin layers on a surface.
A new method developed by a team including researchers from the U.S. Department of Energy's (DOE) Argonne National Laboratory makes ALD possible on nearly any membrane. The researchers discovered a surprisingly simple solution: dipping membranes in tannic acid first. The acid's molecules stick to the membrane's surface, providing nucleation sites—or points where an ALD coating can take hold and grow.
The ability to use this technique on typically resistant membrane materials enables a variety of potential enhancements that could improve functionality and durability—or create altogether new properties. The work is detailed in the paper "Polyphenol-Sensitized Atomic Layer Deposition for Membrane Interface Hydrophilization," which was recently published in the journal Advanced Functional Materials.
Many commercial membranes are made from common plastics such as polypropylene and polyethylene, which are inexpensive and relatively sturdy. But when used to treat water, these polymer-based membranes tend to cause problems. Their surfaces are prone to fouling, where contaminants accumulate in their pores and reduce efficacy.
With ALD, a process common in the semiconductor industry, membranes can be altered to resist fouling or take on other desirable properties. Molecules deposited on the surface can weave their way through a membrane's tortuous network of pores to find all the surfaces inside, creating an exceptionally uniform coating.

"ALD, in principle, is great," said Seth Darling, a co-author of the study and director of Argonne's Advanced Materials for Energy-Water Systems (AMEWS) Energy Frontier Research Center. "The challenge is that most polymers that are used to make membranes are not amenable to coating with ALD."
In the study, tannic acid pretreatment enabled a water-resistant polymer membrane to be coated with titanium dioxide, transforming its surface to become hydrophilic (water-loving) instead. The water-attracting layer creates a protective buffer against fouling.
The AMEWS center, which is funded by DOE's Office of Science, supported the work as part of a broader effort to understand and control what happens at the interface between water and solid materials. Such understanding is key to improving how we process and use water.
In the past, Argonne researchers have exploited the fact that some polymers are inhospitable to ALD by creating a two-faced "Janus" membrane, with a full metal oxide coating on top of the membrane and none on the other side. This latest study is the first time scientists have been able to completely and uniformly sensitize a membrane to ALD using a nondestructive pretreatment.
Argonne is developing methods for scaling up ALD and other interface engineering capabilities so that these methods can be evaluated for large, industrial applications. "We currently use lab-scale reactors for these research studies, but we are building tools for efficient ALD processing of large area substrates. This will allow pilot-scale testing of our ALD materials," said Jeffrey Elam, a senior chemist at Argonne and study co-author.
The new method potentially could work not just with tannic acid but any liquid polyphenol and also with any polymer membrane, which opens up a vast number of possibilities beyond the proof of concept described in the paper. In addition to water-attracting or water-resistant coatings, ALD can be used to create chemically reactive or electrically conductive materials.
"There's a whole library of things you can do with ALD," Darling said. "This technique now opens up that library for polymer membranes."
More information: Xiaobin Yang et al, Polyphenol‐Sensitized Atomic Layer Deposition for Membrane Interface Hydrophilization, Advanced Functional Materials (2020). DOI: 10.1002/adfm.201910062
Journal information: Advanced Functional Materials
Provided by Argonne National Laboratory